Did you scan a QR code to get here?
If you’ve landed on this page because you scanned a QR code on one of our drums that’s great! We’re working behind the scenes to develop a content specific page for each drum, so when you scan you will be able to see how many times that exact drum has been re-used and equating that to how many single-use pieces of plastic and emissions have been saved.
In the meantime, you can read below how we make our business circular and find out our overall combined impact.
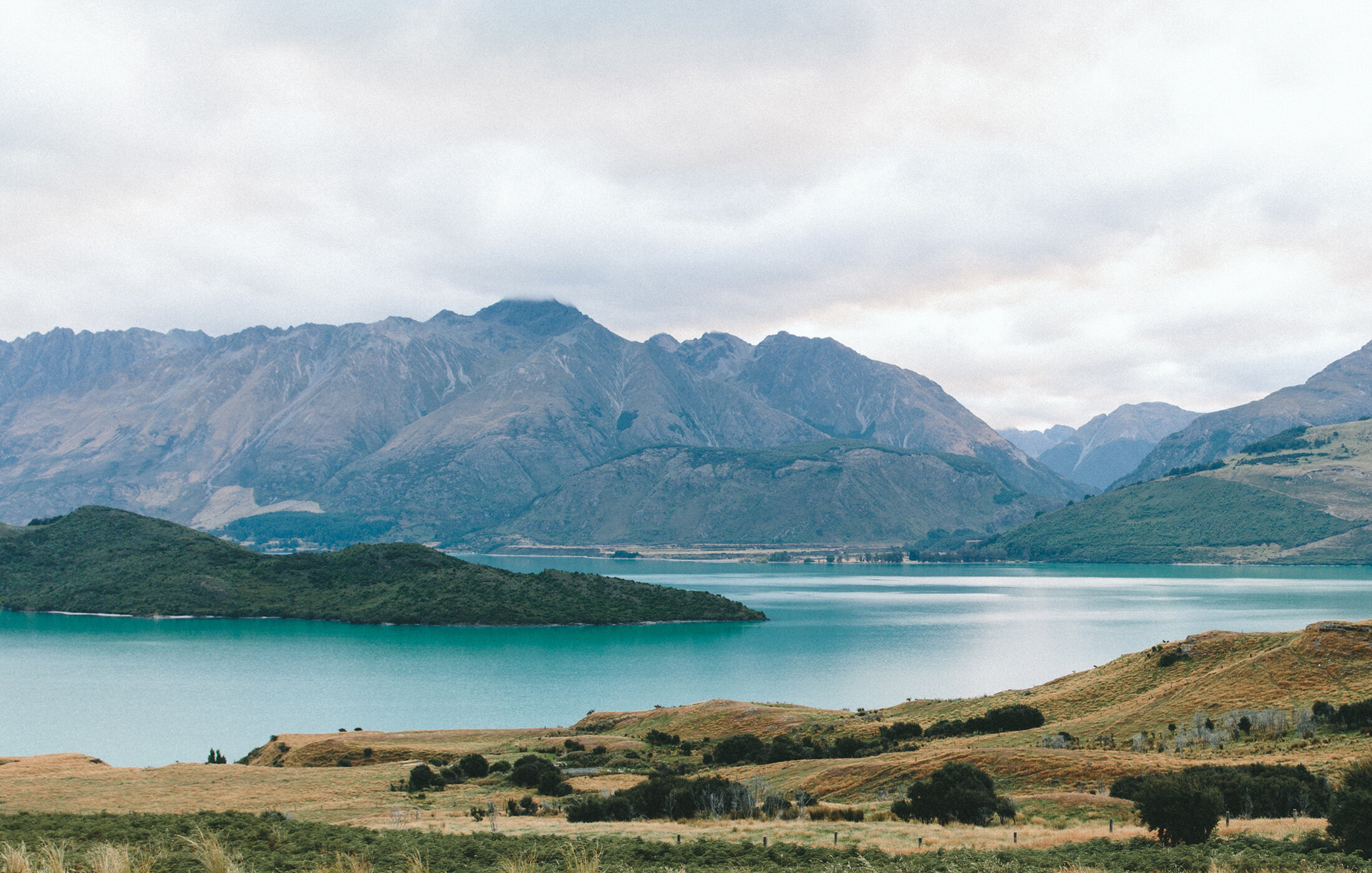
How did we come up with these numbers?
Sing-use plastic saved: we used Ocado to look at all their products in a particular category and calculate what an average size single-use bottle/container would be, then it’s just a simple sum based on our sales, relatively easy
CO2 saved: not so easy to calculate! We’ve based this one purely on tailpipe emissions. We worked out our average mileage per year, and calculated what the diesel version of our van delivering from outside London would produce et voila! Our numbers are based on a Citroën Dispatch 1200kg that has official CO2 rating of 198g/km and MPG of 40.9.
The number we come up with is a conservative estimate as it is just based on tailpipe emissions and does not include emissions saved from single-use plastic being shipped around to recycling centers and the emissions from the recycling process itself (more on that below).
Water saving: this calculation we’re still working on. There can be a perception that cleaning and reusing drums can use more water than recycling. However in order for plastic to be recycled, it has to be washed before it’s bailed, shredded, melted and then turned back into a single-use drum!
So whilst water saving is important, all the other elements of recycling need to be taken into consideration when comparing linear recycling to closed-loop re-use. Here’s some great information about plastics and the circular economy by the Ellen MacArthur Foundation.
We’re working on a detailed life cycle analysis and will be releasing that soon with a few informative blogs.
Reverse logistics helping to close the loop
-
It starts with an IBC
The majority of liquid and cream products will start their life in an IBC after the mixing phase. Intermediary bulk containers (IBC) come in a range of sizes but we tend to get our products from the manufacturers in 1,000 Litres.
Once the IBC is empty, it’s sent back to the manufacturer to be cleaned and reused, keeping the cycle going. Empty IBC’s are collected the same time new full IBC’s are delivered, so optimizing any deliveries that are not yet zero emissions.
-
Filling, filling and more filling!
We use taps and pumps to dispense the liquids into the 10 & 20L drums from the IBC’s. These drums are made up of a mixture of PCR (post-consumer recycled) and HDPE (High-density polyethylene) plastic.
The aim is to reuse every drum over and over again until they are no longer fit for purpose, and then ensure each one is recycled into something else that can be reused again. Some drums have been in circulation with us now for over 3 years!
-
Zero emissions vehicles
We made the conscious decision to focus on a small radius to enable us to do last-mile delivery using our electric vehicles. We also collect empties when delivering, so drums are never posted back to us! As van ranges improve, our delivery radius will expand.
Other benefits of keeping it local is customers can get next day delivery, we can offer no minimum order quantity, and we get to know our customers really well and count a lot of them as friends. The best part of the job.
-
Cleaning drums for refill
To help further lower our emissions output, our container cleaning unit is a second-hand laboratory cleaner.
We modified it slightly to fit our 10L & 20L drums, it can take 12 x 10L drums and up to 6 x 20L drums.
Another energy saving element are the solar panels on our warehouse and we are working on a water saving project, which we’ll hopefully have up and running early 2023.